The goal of supply chain management is to turn raw materials into finished products and move those finished products through the supply chain to end customers as efficiently and profitably as possible. But, as Newton’s Third Law of Motion states, for every action there is an equal and opposite reaction. In supply chain management, that reaction is reverse logistics.
Reverse logistics is a crucial part of supply chain management, focusing on the movement of goods after they reach the end user.
Reverse logistics solutions help businesses recapture value while ensuring environmental compliance. Whether it’s handling customer returns, redistributing unsold inventory, or implementing an efficient reverse logistics system, effective management of these processes enhances profitability and customer satisfaction.
Most consumers don’t think about reverse logistics—until a business mismanages the process. While little known, reverse logistics has a big impact on business success. “When done right,” says former Forbes Councils Member Mahesh Nandyala, “reverse logistics makes it easier for customers to make returns while reducing business costs and enhancing customer satisfaction.”
Reverse logistics “done right” also boosts efficiency and environmental compliance.
Today, we’ll take a deep dive into reverse logistics and how Enterprise Resource Planning (ERP) solutions can help ensure success.
Reverse Logistics Categories
There are two primary categories of reverse logistics: consumer returns and business returns.
Consumer Returns
Customers often return products for three main reasons: defects, dissatisfaction, or a change of mind. However, returns can also occur due to other factors, such as the need for recycling, refurbishing, or specialized disposal that the seller can handle.
No matter the reason, customers expect the return process to be a hassle-free, streamlined experience, and, when it is, they reward the impeccable service with their loyalty.
Business Returns
Businesses or retailers may return products to manufacturers or distributors when the products aren’t selling, when there have been delivery failures, when items have reached the ends of their lives, or when a product has been rented.
By returning such products back through the supply chain, businesses maximize their inventory, minimize waste, and stay in compliance with environmental regulations.
Reverse Logistics Processes
Reverse logistics processes form the backbone of an efficient reverse logistics system. These processes ensure that returned, unsold, or defective products move through the supply chain efficiently. Below are key types of reverse logistics processes businesses should focus on.
Returns Management
Effective returns management is essential for a well-functioning reverse logistics system. It ensures that returned products re-enter the supply chain efficiently while minimizing costs. Implementing advanced reverse logistics solutions helps businesses automate returns processing, manage inventory fluctuations, and enhance the customer experience.
This requires a business to transparently display its return policy and have a system in place to process returns, schedule shipments, approve refunds, re-categorize returns, manage inventory fluctuations, and more.
Remanufacturing and Refurbishment
When products are returned, remanufacturing and refurbishment are two ways to restore their value. For example, if a product is returned due to a defect or flaw, businesses can repair the product with parts from other products or with inventory materials—ultimately reselling it as a modified product.
Packaging Management
This process focuses on efficient packaging and waste reduction. When a returned product cannot be reused, remanufactured, or refurbished, its packaging can be used again for new products.
Handling Unsold Products
Most businesses have agreements in place with their manufacturers or distributors to handle unsold products.
Regardless of why products don’t sell (e.g., outdated merchandise, lack of demand, price concerns, etc.), businesses can cut down on costs and reduce inventory overages by returning the items to the manufacturer or distributor for a credit or refund.
Managing Failures, Rentals, and Maintenance
When a delivery fails, businesses—if staffed and equipped appropriately—can determine why the issue happened, fix the problem, and resend the item to the customer. When a business rents equipment, it is responsible for managing its initial rental agreement and then sub-renting the equipment to its own customers.
Businesses may also enter into product agreements, under which they manage repairs and maintenance; when the agreement comes to an end, the businesses can either recycle or re-rent the equipment to new customers.
The 7 Rs of Reverse Logistics
Successfully managing reverse logistics is crucial, and it begins with understanding and effectively executing the 7 Rs:
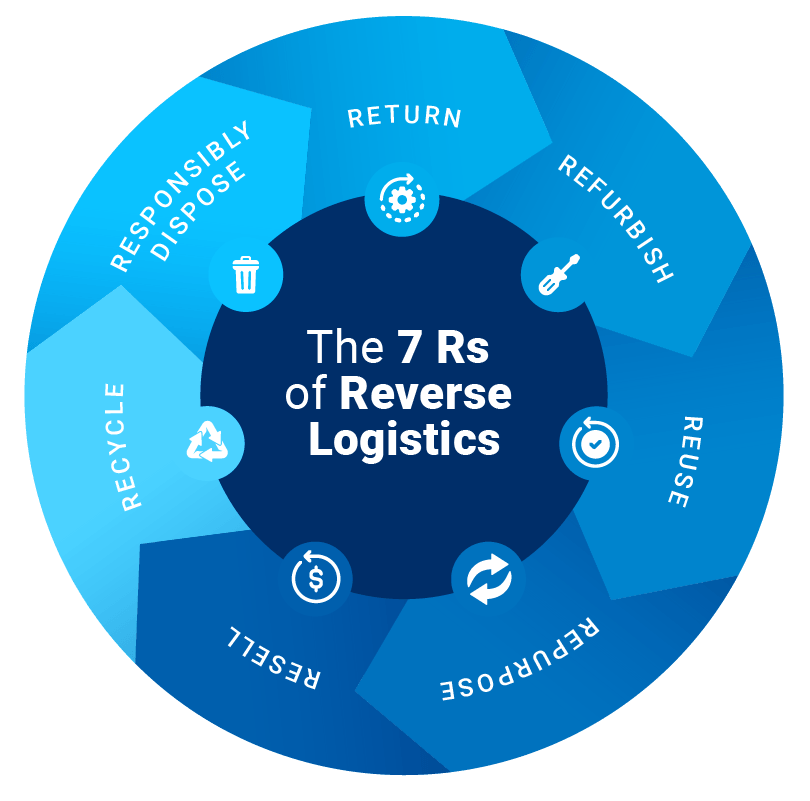
- Return: Having a process in place to smoothly place returned items back into the supply chain
- Refurbish: Inspecting, cleaning, and fixing a product and confirming whether it can be repackaged and sold as a used, competitively priced product
- Reuse: Reusing the components and packaging of returned (unfixable) products for other items, reducing waste and boosting sustainability
- Repurpose: Using each part of a returned product in new, innovative ways—contributing to environmental sustainability
- Resell: Reselling products that have no defects and were returned due to customer preference
- Recycle: Breaking down and properly recycling unfixable products and their components
- Responsibly dispose: Disposing of non-recyclable products in a responsible way—by donating items or following environmental regulations
ERP Systems and Reverse Logistics
Managing reverse logistics effectively requires the right technology. A robust Enterprise Resource Planning (ERP) system enhances reverse logistics management by streamlining operations, tracking returns, and automating workflows. When integrated with supply chain solutions, ERP systems improve visibility across all reverse logistics processes.
Choosing the right ERP solution is essential for optimizing reverse logistics operations, ensuring compliance, and improving profitability
Modern ERP systems deliver centralized business management solutions that connect companies end-to-end: collecting, synchronizing, and delivering data to and from every department in real time.
An ERP (Enterprise Resource Planning) solution offers complete visibility to all team members—based on appropriate access permissions—while also equipping them with the tools they need to automate workflows, facilitate company-wide collaboration and communication, and analyze data.
With a single, sophisticated business management solution, businesses have the technology they need to navigate the forward and reverse logistics of supply chain management. And choosing the right ERP system begins with ensuring that it has these key features:
- Data management
- Warehouse management
- Inventory management
- Order/supply/sourcing management
- Transportation management
- Collaboration tools
- Business intelligence and risk management tools
Conclusion
Managing reverse logistics effectively with an eye towards customer satisfaction and boosting the bottom line begins with the proper technology—technology like Acumatica.
Acumatica rests on a flexible, customizable platform and empowers businesses with the integrated, industry-specific applications they need to manage supply chains, warehouses, orders, and inventories from one place—whether their teams are in the office, working remotely, or on the road.
Acumatica’s ERP software helps small and midsized businesses accept returns, issue refunds, track inventory, transport products, and manage customer data.
Built-in documentation and reports ensure that every team member is informed about the volume of products returned, the associated costs, the condition of returned products, and more. And Acumatica’s fully integrated financial, inventory, and customer management applications mean businesses have the updated, accurate, and real-time information they need to make informed decisions.