In this article:
-
-
- A Practical Guide to Efficient Order Picking
- Order picking in Warehouse: Understanding the Fundamentals
- Core Principles: Accuracy, Efficiency, and Safety
- Finding the Perfect Fit: Different Methods for Different Needs
- Strategies for Effective Order Picking
- Order Picking: The Link to Operational Efficiency and Happy Customers
-
A Practical Guide to Efficient Order Picking
Distributors, manufacturers, and retailers understand the importance of order picking and its impact on warehouse operations. And, working in one of these industries, you know first-hand that today’s customers expect accurate, on-time, and low-cost shipments.
Such expectations can only be met with disciplined, detailed inventory management and by equipping your warehouse team with the tools they need to pick, pack, and ship orders quickly and accurately.
Your order picking process must be on point to make your business more efficient and to better serve your customers.
This guide will help you master order picking by providing an in-depth look at the core principles of order picking, different order picking methods, and the role technology plays in enhancing the process.
Order picking in Warehouse: Understanding the Fundamentals
Order picking is the act of retrieving products from warehouse locations to fill each customer’s order.
Though it sounds simple, it’s anything but.
Successful order picking requires:
- a fully stocked and inventoried warehouse
- a defined picking strategy
- order-picking tools and technologies
- trained warehouse workers.
Modern order picking software and multi order picking systems help streamline these operations.
Order pickers use a pick list to direct them to varied locations in the warehouse to find products from the list. Depending on the level of automation your warehouse employs, order pickers may walk miles daily, lift heavy and cumbersome products, and push heavy carts.
These employees must be able to endure sustained physical activity, and your company must adhere to the three core principles of order picking: Accuracy, Efficiency, and Safety. Implementing proper order picking procedures and maintaining high order picking accuracy are crucial for success.
Core Principles: Accuracy, Efficiency, and Safety
Accuracy
Selecting the right product at the right quantity for the right order is critical. If an order picker doesn’t pick an order correctly, they’re forced to retrace their steps, put the items back, and find the correct items, which can delay schedules. If they don’t catch the error and the customer receives the wrong product, then your business must cover the cost for returns and refilling the order. Unfortunately, your customer may be dissatisfied with your service—even if the mishap occurs only once—and take their business elsewhere.
Efficiency
You can ensure efficiency by improving warehouse layouts for easy navigation (e.g., wide aisles, well-lit work areas, and posted traffic flows). You must also keep your inventory up-to-date, ensure that it is easily located, and clearly define your order picking process. When your business runs smoothly, your customers and your executives watching their bottom line are happy.
Safety
You rely on your employees to do their jobs, and they rely on you to keep them safe. A safe workspace includes proper forklift, material-handling, and warehouse activity training. It also means that you provide tools required to complete warehouse activities (e.g., hand trucks, carts, and motorized platforms). Safe environments provide ample time for workers to stretch and rest. Just as efficiency leads to happy outcomes, so does a safe and healthy working environment.
Ultimately, an accurate, efficient, and safe order picking process enhances inventory management, reduces operational costs, and improves customer satisfaction. But to get to this point, you must first find which order picking method is the most effective for your business.
Finding the Perfect Fit: Different Methods for Different Needs
Every business is different. Some businesses fall into the small and midsized category, filling dozens, hundreds, or thousands of orders a day, while larger businesses fill millions of orders a day (think Amazon). As such, each business requires an order picking method that can accommodate its specific needs.
Order Picking Methods
Single Order Picking: Focused and Precise
Single order picking (or discrete picking) tasks order pickers with filling one order at a time. Their pick list includes the SKUs for a single order, and, after retrieving each item on the list, they deliver the items to the packer for shipping. The picker is then free to begin the next order. This method is simple to learn and is a great choice for smaller warehouses with fewer orders.
Batch Picking: Power in Numbers
In batch picking, order pickers find items from multiple orders that are stored in the same area of the warehouse. They deliver the batched items in carts or bins to be sorted, packed, and shipped. This method reduces travel time and works well for high-volume warehouses with many small orders.
Wave Picking: The Harmony of Single and Batch
Wave picking combines the benefits of single and batch picking. Orders are scheduled in “waves,” which means the lists are consolidated so that the pickers can pick them in one pass, organizing them into totes as they go. This method balances the workload between pickers and works well for medium to large-sized warehouses.
Zone Picking: Conquering Vast Warehouses
In zone picking, order pickers work in specified warehouse zones. Orders are organized by zone, which allows pickers to pick SKUs for multiple orders in their zones only. The order then moves sequentially through different zones. This method allows for multiple sets of eyes to check each order during preparation, improving accuracy. It also helps reduce each picker’s amount of walking time and is appropriate for businesses with larger warehouses that have the technology to sort their orders accordingly.
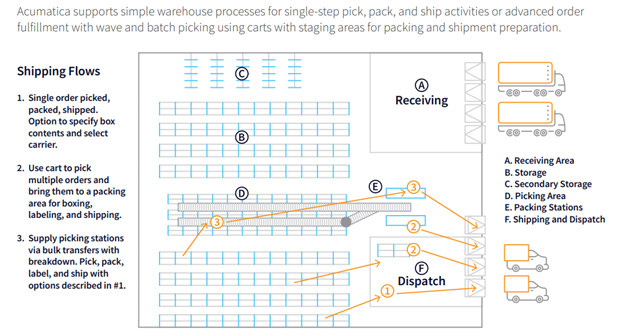
Strategies for Effective Order Picking
So, what are the best strategies for ensuring your order picking is as effective as possible? There are a few.
For example, you’ll want to optimize your workflows. This can include streamlining every step via a well-thought-out order picking plan, providing a smart—and safe—warehouse layout, and offering employees detailed, ongoing training.
Another strategy is to use automated solutions that help reduce physical labor and human error. Examples include automated guided vehicles (AGVs), collaborative robots (cobots), and voice-directed picking systems.
You may also consider hiring warehouse consultants to recommend changes to warehouse layouts.
Another way to improve picking accuracy is to clearly mark every storage location in your warehouse with location tags. This includes zones, aisles, racks, shelves, bins, and other locations.
Again, warehouse consulting professionals are beneficial to recommend the best locations for items based on frequency of orders (inventory hits), weight or dimensional constraints, items that are commonly selected for similar customer orders, and other criteria.
Implementing order picking software in the form of a complete enterprise resource planning (ERP) system with an embedded warehouse management solution (WMS)—like Acumatica—is another smart strategy.
Our comprehensive ERP solution offers you the ability to streamline fulfillment, reduce errors, and increase warehouse productivity. Specifically, our integrated ERP and WMS solution features paperless picking options and prioritized picking queues.
Minimize data entry errors with barcode scanning and access role-based dashboards that keep warehouse managers on top of what’s happening across their facilities. Larger and more complex warehouse environments are served by one of many connected WMS applications that work seamlessly with Acumatica’s inventory and order management applications.
With Acumatica, your centralized access to companywide data, combined with sophisticated analytical tools, will help you make strategic, business-building decisions.
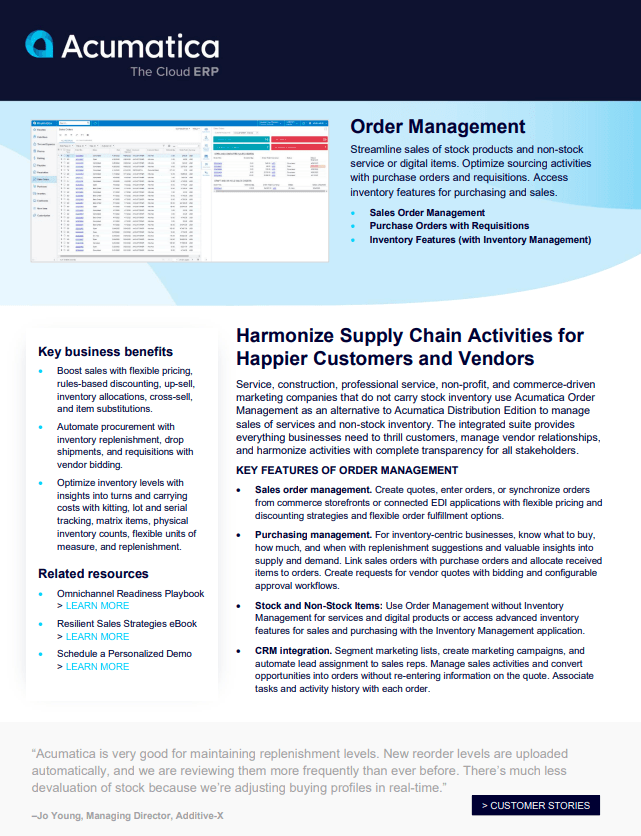
Download Order Management Product Sheet
Order Picking: The Link to Operational Efficiency and Happy Customers
Operational efficiency and happy customers are possible when you have an effective order picking system in place. Order picking is an essential step in the supply chain, and, when orders are handled with speed and accuracy, your business is well on its way to finding long-term success.
Let Acumatica be your partner in order-picking excellence. Our cloud ERP solution and integrated WMS can help you streamline your warehouse operations and transactions by combining the power of our order management and inventory management applications. Together, they provide every order-picking feature you need, from eco-friendly, efficient paperless directed picking, wave/batch picking, barcoded pick lists, and packing automation to bidirectional picking, prioritized picking queues, role-based dashboards, and everything in between.
According to Ben Leinster, CEO of AFF|group, Acumatica’s order picking software is exactly what they needed. “For us, the power of the Acumatica system is in the WMS and shop floor data collection, the inventory management, the ability to deliver to a customer and to get things right.”
Warehouse Manager Dashboard
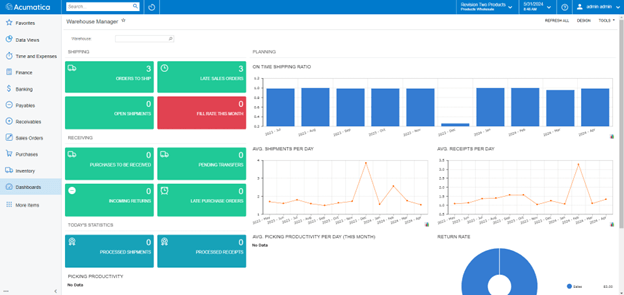